Precast Concrete Cost Vs. Value: Is It Worth It?
In today’s quick-moving construction world, picking the right materials and methods can really make or break a project. Precast concrete has emerged as a preferred solution for many builders and developers, yet a critical question remains: Is the investment justified? By examining precast concrete’s value proposition—including costs, efficiencies, and long-term benefits—we can explore why it could be a strategic decision for your upcoming builds.
Understanding Precast Concrete Cost Factors
The cost of precast concrete isn’t a simple price-per-unit calculation. Several key factors influence the final price:
Manufacturing Infrastructure
Making precast concrete requires advanced setups. These facilities come with specialized machines, precise molds, and controlled climate conditions. All this careful management not only helps maintain quality but also makes the initial costs higher. While it seems like a lot to invest in fancy equipment and facilities upfront, it pays off in the long run with better product quality and consistency.
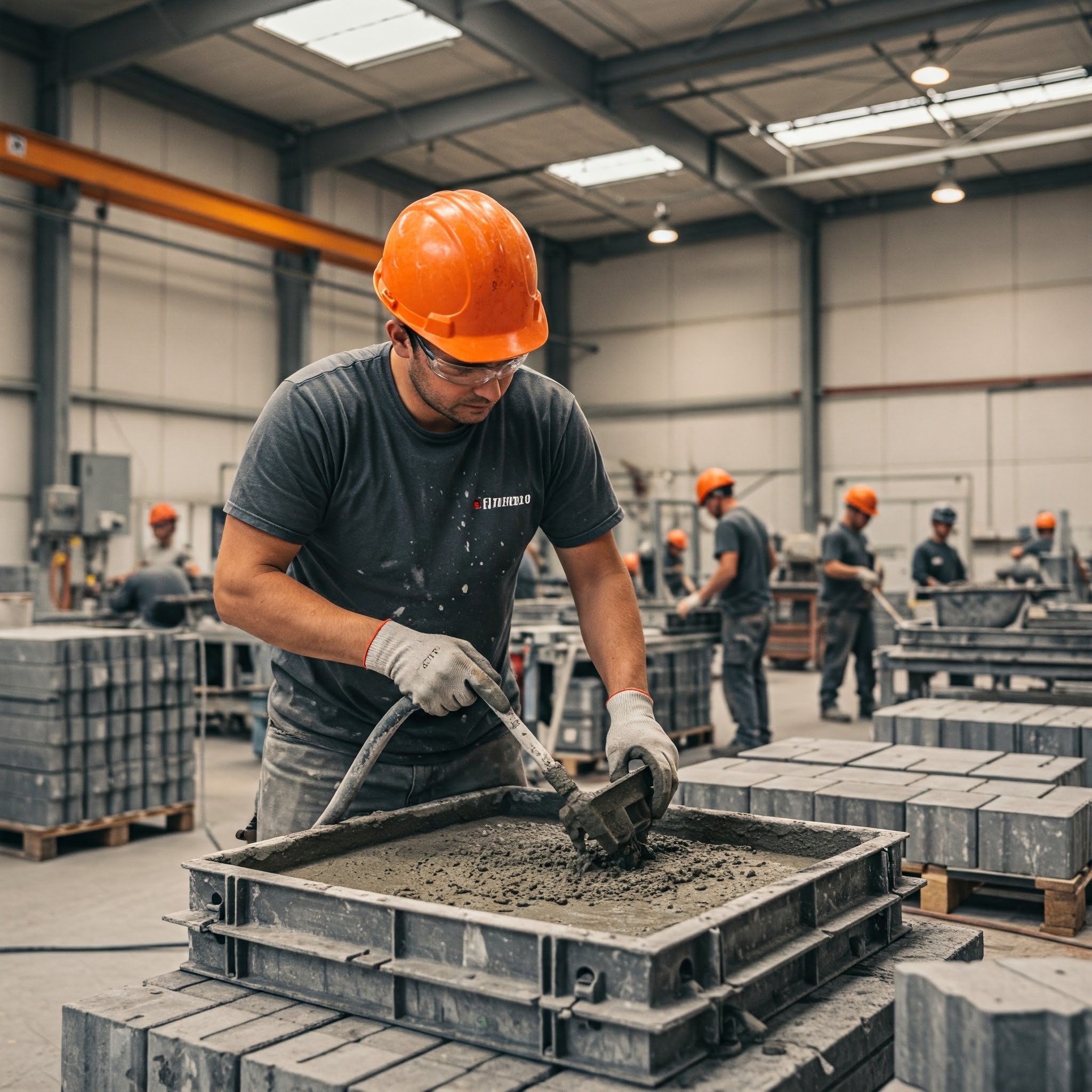
Labor and Expertise
Skilled workers and experienced engineers are crucial when it comes to making precast concrete. Sure, their skills might cost a bit more, but that investment pays off with better quality products with fewer problems and lasting longer. Plus, working in a factory means they can keep producing all year round without being held up by bad weather, unlike the usual concrete work done on-site.
Material Costs
Precast concrete is made up of three main ingredients: cement, aggregates, and reinforcement materials, which can all be affected by market ups and downs. But buying in bulk and using materials efficiently in a factory setting usually helps keep costs down. Plus, being able to adjust mix designs and maintain strict quality control is super important for making sure everything is durable and performs well.
Transportation and Installation
Transporting precast components from the factory to the job site requires specialized equipment and careful logistical planning. Although transportation costs can be quite high, particularly for larger elements or over long distances, these expenses are often offset by lower on-site labor needs and quicker installation times.
The Value Proposition Explained
Although the upfront of the precast concrete cost may appear higher than that of traditional cast-in-place methods, it provides several advantages that can optimize the overall budget of the entire project and significantly enhance its long-term value.
Accelerated Construction Schedules
In the construction industry, time is money, and precast concrete provides significant time savings. Since precast components arrive ready for installation, the risk of delays due to weather conditions is greatly reduced. Additionally, multiple activities can take place simultaneously, leading to a more efficient workflow. Completing the project earlier not only shortens the overall timeline but also ensures a quicker return on investment.
Reduced Labor Costs
Although precast concrete may involve higher initial costs, it can lead to significant savings in overall labor expenses. This approach requires fewer workers on-site, minimizes the risk of weather-related delays, and decreases safety hazards thanks to controlled installation processes. Additionally, there are fewer demands for formwork and cleanup, making the whole process more efficient.
Quality and Durability Benefits
A controlled manufacturing environment leads to the creation of exceptional products, offering several key advantages:
- Uniform strength and appearance
- Enhanced durability against weathering and wear
- Decreased maintenance needs
- Prolonged service life
- Fewer warranty claims
Environmental and Sustainability Advantages
Precast concrete provides a range of environmental advantages that can lead to significant cost savings:
- Minimizes waste through efficient production techniques
- Reduces energy consumption during installation
- Improves thermal performance in completed buildings
- Offers the possibility of earning LEED certification points
When Does Precast Concrete Cost Make Financial Sense?
Precast concrete proves to be a highly cost-effective option in several key situations:
- Fast-track projects where meeting deadlines is essential
- Structures that demand exceptional durability or specific performance characteristics
- Projects located in regions with elevated labor costs or shortages of skilled workers
- Applications that prioritize quality and consistency above all
- Buildings that aim for superior energy efficiency
Making the Decision
To evaluate whether precast concrete is the right choice for your project, consider:
Total Project Costs
Look beyond initial material costs to include:
- Installation time and labor
- Equipment requirements
- Schedule impacts
- Maintenance needs
- Expected service life
Project-Specific Factors
Consider your unique circumstances:
- Local labor availability and costs
- Weather conditions and seasonal constraints
- Site access and logistics
- Quality requirements
- Schedule constraints
Conclusion
While the initial precast concrete cost might seem higher than some alternatives, its true value lies in the long-term benefits it delivers. Faster construction, reduced labor needs, exceptional quality, and unmatched durability often make precast concrete the most cost-effective choice over the project’s lifespan.
Why Choose Stonehenge Architectural for Your Precast Concrete Needs?
Stonehenge Architectural is your trusted partner for precast concrete solutions. We bring a unique combination of expertise, craftsmanship, and commitment to quality that sets us apart:
- Decades of Experience: Our team has a deep understanding of precast concrete design, engineering, and manufacturing, ensuring your project is in expert hands.
- Uncompromising Quality: We use only the finest materials and adhere to strict quality control standards to deliver exceptional results that exceed expectations.
- Customization: We specialize in crafting custom precast solutions tailored to your project’s unique requirements, ensuring a perfect fit and seamless integration.
- Sustainability: We are committed to sustainable practices, minimizing waste and using eco-friendly materials whenever possible.
- Exceptional Service: Our dedicated team provides personalized support throughout your project, from design and engineering to manufacturing and installation.
When you choose Stonehenge Architectural, you’re not just choosing a precast concrete supplier; you’re choosing a partner invested in your project’s success. Contact us today to discuss your vision and discover how our precast concrete solutions can elevate your next construction endeavor.